Computational and Multiscale Mechanics of Materials (CM3) – University of Liege
The Computational and Multiscale Mechanics of Materials unit has been created in 2008 by Prof. Ludovic Noels with the aim of proposing multiscale numerical methods to predict the behaviour –including failure– of structures made of complex engineered materials.
Through collaborative projects, the unit has developed an acknowledged expertise in
- The development of multiscale methods for complex non-linear material systems. In particular efficient algorithms for computational homogenisation and mean-field homogenisation methods were developed and implemented in a parallel setting in the open source finite element code Gmsh.
- The propagation of damage and fracture across the different length-scales. The unit has extensively developed multiscale methods considering the failure in composite laminates through a damage-enhanced mean-field homogenisation scheme and computational homogenisation. In particular, since the Representative Volume Element does not formally exist when involving fracture, the method objectivity is carefully studied.
- The propagation of buckling instabilities across the different length-scales. Propagation of micro-buckling in cellular materials was captured through second-order computational homogenisation.
- The propagation of stochastic effects in thermo-elasticity across the different length-scales by defining and combining Stochastic Volume Element realisations, the construction of a stochastic model to generate a meso-scale (spatially correlated) random-field of the homogenized material properties, and structural-scale stochastic finite elements.
- The construction of surrogate models in stochastic multiscale approaches: micro-mechanics based surrogate models for non-linear composites, neural networks as surrogate of meso-scale BVP, polynomial chaos expansion-based surrogate model for non-linear physical behaviours etc.
- Bayesian inference in order to identify non-linear multiscale models parameters and to construct stochastic multiscale models.
Applied Mechanics and Mathematics (MEMA) – Université Catholique de Louvain
The Applied Mechanics and Mathematics (MEMA) Division develops mathematical models, computer simulation methods and software for the theoretical prediction of the behaviour of solids and fluids. The Division has five permanent members of academic staff, and about 30 Ph.D. students and post-doctoral researchers. Research topics concern: granular flow, suspensions, turbulence, environmental flow, composite materials, metal forming, damage mechanics, oceanography, finite element methods, meshing methods, etc.
Within the MEMA Division, the focus of Prof. Issam Doghri’s group is on the development of nonlinear constitutive models of solid materials both at the macroscopic scale and homogenisation-based. The objective is to propose rigorous and efficient models and algorithms for homogeneous and heterogeneous materials (e.g., composites with a polymer matrix reinforced with short, long, or continuous fibres; porous materials). I. Doghri and his group have worked on:
- Constitutive models for thermoplastic polymers coupling viscoelasticity, viscoplasticity, and damage;
- Mean-field homogenisation of elasto-plastic and elasto-viscoplastic composite materials, and finite strain mean-field homogenisation of composite materials with hyperelastic-plastic constituents;
- Micromechanical modelling of the deformation and damage of short fibre reinforced thermoplastics;
- Multiscale modelling of continuous fibre reinforced composite structures based on a nonlocal damage matrix model;
- Multiscale model for high cycle fatigue of neat / short fibre reinforced thermoplastics;
- Time and space (« 4D ») homogenisation of homogeneous and reinforced viscoelastic-viscoplastic solids under large numbers of cycles;
- Effective yield criterion for porous materials with Hill’s orthotropic matrix based on static limit analysis;
- Full-field finite element (FE) analysis of representative volume elements (RVEs) for composite and porous materials;
- Extension of the coupled viscoelastic-viscoplastic constitutive polymer model to large deformations and anisotropy (PhD thesis of Gudimetla & publications);
- Coupled viscoelastic-viscoplastic modelling of thermoplastic polymers;
- Thermomechanical coupling of viscoelastic-viscoplastic response of thermoplastic polymers
- Homogenization models for porous and composite materials
- Coupling full-field and mean-field homogenization methods for nonlinear multiphase materials; Modeling of polymer material transformation during SLS additive manufacturing process.
Multiscale Materials Modelling – IMDEA Materials Institute
IMDEA Materials Institute (Madrid Institute for Advanced Studies of Materials, IMDEA) is a non-profit independent research institute promoted by the Madrid regional government in year 2008 to perform research in Materials Science and Engineering. IMDEA is committed to three main goals:
- Excellence in Materials Science and Engineering research;
- Technology transfer to industry to increase competitiveness and maintain technological leadership; and
- Attraction of talented researchers from all over the world to Madrid to work in an international and interdisciplinary environment.
The Multiscale Materials Modelling (MMM) group is a research group part of IMDEA Materials Institute, Madrid, led by Prof. Javier Segurado, Senior Researcher at IMDEA Materials Institute and Professor at the Technical University of Madrid. The research group aims at
- Developing models to predict the mechanical behavior and microstructure evolution of heterogeneous materials as a function of their microstructure;
- Studying various material systems ranging from metals to polymers;
- Developing numerical tools such as homogenization, crystal plasticity, dislocation dynamics, phase-field, Finite Element method and Fast Fourier transform based solvers. ;
- Conducting experimental studies in nano-indentation, FIB, SEM and TEM microscopy and different techniques for in-situ testing.
Institute for Polymer Product Engineering (iPPE) – Johannes Kepler Universität Linz
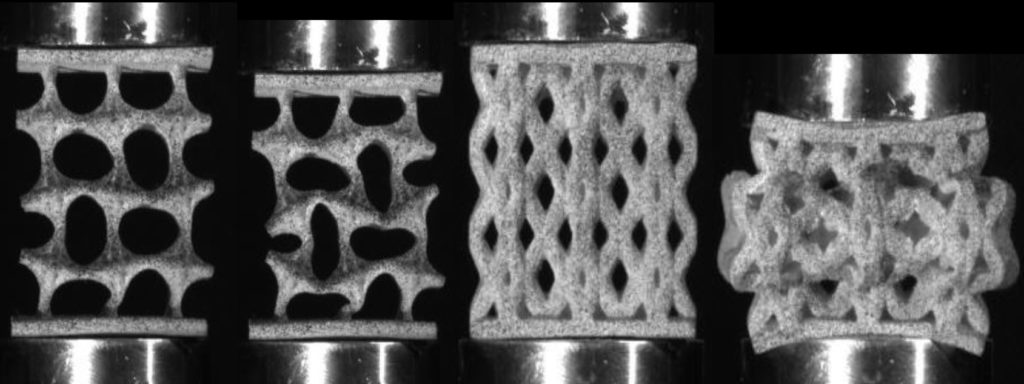
The Institute for Polymer Product Engineering (JKU-IPPE) was established in 2009 in the frame of the Polymer Technology and Engineering Program at the Johannes Kepler University (JKU) Linz. The institute places its main education and research activity on the field of design with polymeric materials and polymer product engineering in close cooperation with other institutes of the Polymer Program. In general, the institute deals with the various aspects of the structural integrity assessment for polymeric materials and with the design of parts and components made from polymeric materials. In addition to the application of conventional structural polymeric materials, special emphasis is devoted to novel multifunctional, smart polymeric materials for advanced engineering applications.
The research of the institute focuses on the:
- Characterization of time and loading rate dependent deformation and failure behaviour under complex multi-axial loading situations, determination of material parameters for simulation models and laws development and conduction of component tests;
- Development and implementation of integrative simulations of polymeric components – engineering molecular dynamics – processing – micromechanics – structural behaviour and reliability and life time assessment;
- Application of heterogeneous and hybrid materials and composites at various length scales for components;
- Comprehensive design of polymeric components from a material micro to a component macro scale;
- Additive manufacturing of conventional and smart polymeric materials on nano-micro and macro-scale for engineering (soft robotics, establishment of a Locomotion Lab in LIT Open Innovation Centre) and medical (medical models for treatments and education) applications.
cirp GmbH
cirp GmbH, founded in 1994, is a German company located in the southwest state of Baden-Württemberg. It is a well-known service provider for the production of prototypes and small-run series in the field of additive manufacturing. It works mainly in B2B relation with a wide range of industrial sectors (automotive industry, mechanical engineering and medical technology among others). Apart from that, cirp has a programme of 3D-printed luminaires and hosts the purmundus challenge – an annual international design competition for 3D-printed products.
cirp’s expertise is to process polymers by additive manufacturing. The company generates more than 50% of its turnover with additive manufactured parts and products and has grown substantially over the last years thanks to the effort and enthusiasm to keep up with the market demands and innovations. In this regard, research is a key-element and cirp plays an active role in joint research projects.
Since 1998, cirp has participated in diverse funded research activities covering from a regional and a national scale up to large European collaborative projects with international partners. The company has gained an insight into the latest technological innovations, solid experience in project and financial management, and deep knowledge on polymer processing in additive manufacturing and in injection moulding as well.
It has established itself as a pivotal player and trusted partner creating a connection between the market demands in the industry and the latest breakthrough technology. With these research activities, the company contributes to push the boundaries of additive manufacturing and improve not just the materials, but also the process robustness. The qualified personnel is capable of modifying and building special equipment.